INNOVATIVE TUBULAR HYDROFORMING
Revolutionizing Metal Fabrication.
As pioneers of tubular hydroforming in the appliance industry, we transform complex multi-part assemblies into lighter, stronger, and more dimensionally stable components. Our method, which has fewer steps than stamping or welding, makes design more flexible by allowing large radius bends, changes from circular to elliptical shapes, cross-sections with multiple faces, and variable diameter expansions of up to 35%.
benefits
- Weight and component reduction.
- Superior bending strength and torsional rigidity.
- Flexible design and engineering options.
- High stiffness-to-weight ratio with low unit costs.
- Ability to work with thin-walled tubing.
- High-quality surface finishes.
common applications
- Appliance handles.
- Automotive exhaust components.
- Bicycle frames.
- Automotive engine cradles.
- Sink faucets.
- Handrails.
- Chair and table legs.
- Medical instruments.
- Rifle scopes.
- Sporting goods.
process & equipment
- Combines multiple parts into one, reducing weight and complexity.
- Machines capable of up to 1,000 tons of force.
- Maximum bed size of 120″ x 60″.
- Operating pressures up to 30,000 PSI on most machines.
COST-EFFECTIVE
TUBE STAMPING
Maximizing Strength, Minimizing Costs.
Our innovative tube stamping process produces complex tubular parts with superior strength-to-weight ratios, achieving cost savings of up to 30% compared to traditional methods. This technique enables unique design features without added machining expenses.
benefits
- Class A finishes.
- Cost savings and weight reduction opportunities.
- Highly complex tubular shapes and parts.
- Varying shapes (round, oval, square, etc.) and diameters.
- Value-added features such as fasteners can be installed during the stamping process.
- Aesthetic design features such as hemmed edges and coined shapes.
common applications
- Open, diagonal and overlap seams
- Angular ends
- Complex trims
- Special shapes
- Flanged or nosed-in ends
- Notches
- V-joint
- Handles
process & equipment
- Clearing Niagara 400-ton mechanical press.
- 60X120 bed
- 12″ stroke, 42″ shut height, 36″ window CHS coil line.
PRECISION
ROLL FORMING
Engineered for Efficiency, Designed for Versatility.
Our roll-forming process creates strong, lightweight parts with exceptional precision and cost-effectiveness. Ideal for OEMs, we transform ferrous and non-ferrous metals into hardened components, reducing weight and labor costs. With inline sweep and arc rolling capabilities, we produce complex geometries for diverse industries, including automotive, appliances, retail displays, and more.
BENEFITS
- Replace higher cost plastics and extruded parts
- Reduce waste, secondary operations, and labor costs
- Compatible with both ferrous and non-ferrous metals
- Fabricate finished or painted parts
- Broad range of geometric opportunities
COMMON APPLICATIONS
- Appliance and automotive trim
- Data server racking
- Solar frame support
- Slide tracks
- Window frames
OUR EQUIPMENT
Engineered for Efficiency, Optimized for Savings.
We enhance manufacturing efficiency with a streamlined, in-line process that minimizes part handling and reduces costs. We maximize your savings and optimize resource allocation by strategically utilizing existing tooling across multiple parts.
- Supports up to 22 sets of rolls
- Handles materials with a maximum thickness of 0.062″
MillS Products can produce stampings with progressive or hand transfer tooling.
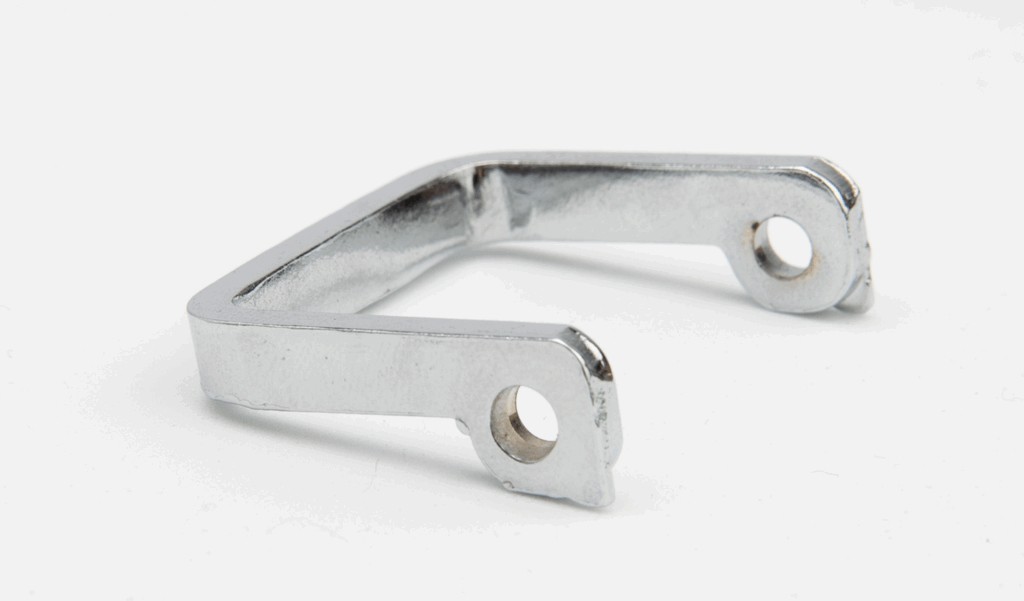
our capabilities
- Equipped with two 400-ton press lines, each capable of handling 36-inch coil widths.
- Supports stamping of a variety of materials such as cold roll and stainless steel.
common applications
- Complex stampings and value-added processes such as powder coating, welding and subassemblies.
processes
- Offers in-line processes that reduce secondary operations, minimizing waste and lowering production costs.
Aluminum Extrusion Finishing: Transforming Extrusions into Exceptional Components.
As a turnkey manufacturer, we deliver cost-effective solutions, taking your raw aluminum extrusions and transforming them into high-quality finished parts. We provide complex forming capabilities and achieve premium surface finishes, including superior Class A surfaces trusted by leading OEMs.
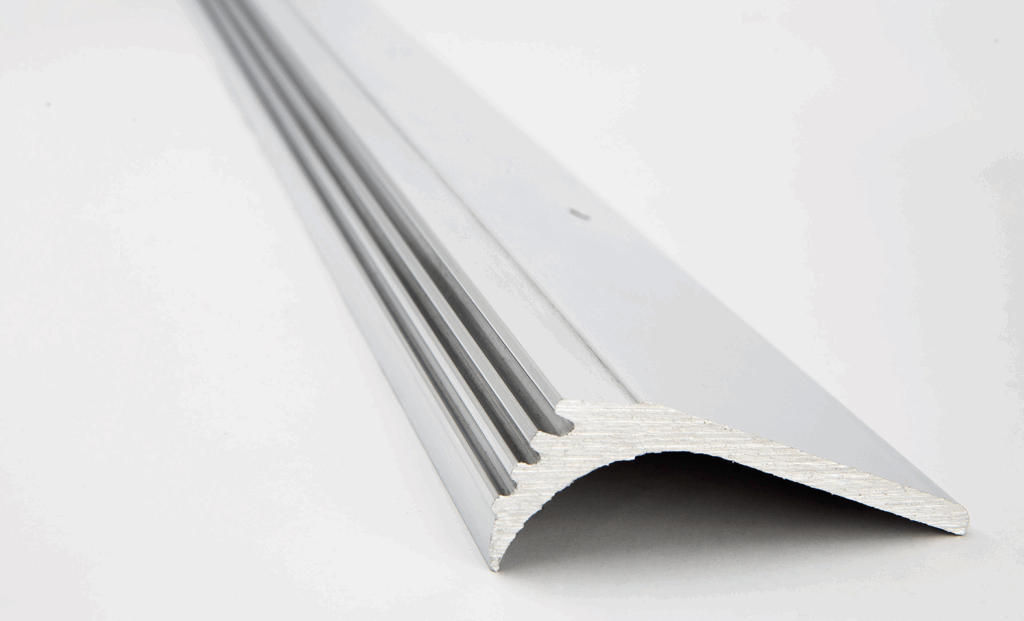
OUR CAPABILITIES
- Secondary Process: Drilling, tapping, punching, automated deburring, sanding, and more.
- CNC Machining: Fully integrated prototyping, including 3D modeling and production CNC machining.
- Finishing: High-quality powder coating, brushing, and polishing.
common applications
- Premium trims for refrigerator shelving and other appliances.
- Appliance handles.
- Automotive trim.
- Elevator handles.
- Strong, lightweight extruded frames and structures for solar panels.
- Extruded components for airport belt stanchions and crowd control barriers.
process & equipment
- High-volume custom powder coating facility: Achieves superior aesthetics and multi-color matching to design specifications and offers corrosion and temperature resistance.
- Two Fadal VNC 4020 Vertical Machining Centers: Max part size: 40” x 20” x 20”.
- One Fadal VNC 6030 Vertical Machining Center: Max part size: 60” x 30” x 30”.
- In-house 3D modeling capabilities.
- Tubular Hydroforming:
- Largest process machine: 1,000 tons.
- Largest bed size: 120″ x 60″.
- Maximum capacity: 30,000 PSI.